The powered height access equipment sector is increasingly developing intelligent technological solutions to prevent operators from acting in an unsafe manner and alert others to dangerous situations – and major contractors are now driving their take-up by mandating their adoption on sites.
Features
How intelligent systems are preventing falls from height
According to the IPAF (International Powered Access Federation) Report 2024, falls from height remain the leading cause of fatal injuries in UK workplaces when working at height. This has been the case since IPAF began collecting such data back in 2012.
Despite improvements in safety culture and growing awareness in the industry, incident rates involving mobile elevating work platforms (MEWPs) are still higher than they should be. Of course, education and training play a critical role, and it’s important that we consistently invest in both of these. However, the industry must face a difficult truth: while behavioural change is essential, it is not sufficient on its own.
Nationwide Platforms’ intelligent anchor point, Harness ON™. Photograph: Nationwide Platforms
After decades of investing in policies, procedures and awareness campaigns, we still see MEWP operators bypassing harnesses, overriding safety warnings or making split-second decisions with catastrophic consequences. Why? Because we’ve placed too much reliance on individuals.
Awareness and training remain vital, but they have limits, especially in high-pressure environments where even experienced professionals can make mistakes. At Nationwide Platforms, we care deeply about behavioural competence; but in training 20,000 MEWP operators per year, we recognise that even the best-trained professionals are human.
Most unsafe acts are not the result of wilful neglect but of routine habits: decisions made quickly, under pressure or with the best of intentions, without systems in place to mitigate against them. These are lapses rather than rebellions. When judgment falters in this way, it’s the system that should step in, not the stretcher.
System flaws
Safety theorist James Reason, in his widely cited ‘Swiss cheese’ model, argued that accidents are rarely caused by a single failure or bad actor. Instead, they result from multiple, often latent weaknesses in a system. Focusing solely on individuals, he warned, distracts from addressing those systemic flaws. Fred Manuele, writing in Professional Safety, similarly critiques the traditional emphasis on “unsafe acts”, and calls for a shift towards system-level interventions, designing safety into work processes, rather than layering it on top.
In all of these cases, the logic is the same: the most reliable safety improvements are not achieved by perfecting human behaviour, but by designing systems that are resilient to its imperfections, and then implementing those systems at pace, collaboratively, across the industry as a whole.
Nationwide Platforms deployed Harness ON for complex applications at the ICE exhibition 2024
In fact, through the ingenuity and collaboration of manufacturers and providers, we’re already starting to see some of the innovations we need.
One such collaborative endeavour between Nationwide Platforms, Dingli, Balfour Beatty and Control Dynamics Inc, led to the development of Harness ON™, a system designed to ensure proper harness use through simple but effective automation.
The system uses an inductive sensor built into the MEWP’s harness anchor point, which connects with a wearable component integrated into the operator’s lanyard. Unless the lanyard is correctly clipped into the designated anchor point on the machine, the MEWP will not function. In practice: no click, no power. This approach removes the need for reminders, signage or supervision, making safe behaviour the only way to operate the equipment. Importantly, it adds no complexity to the operator’s workflow. Clipping in becomes as instinctive as turning the key.
Misuse of safety systems
Of course, no system is entirely immune to being misused, and some operators may try to ‘trick’ a system designed to save their lives; for example, they might try to override the Harness ON™ device by clipping in a spare carabiner from a harness they’re not actually wearing, effectively tricking the system without being properly secured. But these technologies are not designed to override willpower or to police intent. The principle is similar to that of seatbelts: people can still bypass them, but their introduction has saved lives on a massive scale – reducing the risk of death in a vehicle crash by up to 50 per cent for drivers.
If someone is determined to put themselves and others at risk, no system can fully prevent that. What systems like Harness ON™ are designed to do is eliminate the possibility of genuine human error, the kind that happens when someone forgets, assumes they’re fine ‘just this once’, or acts out of habit. For the operators who want to work safely, systems like Harness ON™ make that the default. For the operators who do not want to work safely – who actively seek to undermine even the simplest interventions – the question is not how the system has failed, but whether that individual should be operating equipment at all.
Shift towards intelligent systems
Harness ON™ is part of a wider MEWP industry shift towards intelligent systems built to intervene automatically when risk arises, rather than relying on human reaction alone. For instance, Haulotte’s FASTN system and Niftylift’s ClipOn devices similarly aim to ensure that the operator is clipped in, utilising visual and audio cues that warn the operator and surrounding personnel that they haven’t clipped in.
Entrapment prevention is another area where proactive design is mitigating for human error. Nationwide Platforms has produced the SkySiren® system, a secondary guarding solution originally developed for boom lifts. It halts machine movement if the operator becomes trapped against the controls, and alerts colleagues, such as an ‘on the ground buddy’, that an incident has occurred, enabling them to swiftly come to the operator’s aid.
SkySiren PCS has been custom-built for individual scissor machines. Photograph: Nationwide Platforms
The system has since been enhanced with pre-crush sensor technology, where ultrasonic sensors detect potential entrapment hazards before they can occur. The system stops the machine and alerts the operator, allowing them to make a safe decision about the most suitable course of action. This proactive combination, known as Intelligent Secondary Guarding, has helped reduce boom-related incidents across the industry.
Recognising the rise in scissor lift entrapments, Nationwide Platforms has since developed SkySiren PCS for Scissors, adapting the same intelligent intervention model. The system uses ultrasonic sensors to detect obstructions at all times – even while raising the platform or driving the scissor lift with the platform raised – stopping the machine before a crush incident can occur. Though not formally launched, it is already being used by customers mandating secondary guarding on scissors and is being deployed on a project-by-project basis.
The wider market is responding too, with a range of intelligent solutions for scissors offering varying degrees of intervention. For example, Dingli offers a system for scissor lifts that detects overhead obstacles while the platform is being raised or lowered, and stops movement if a hazard is detected above the operator.
Similarly, EQSS offers an entrapment prevention system specifically designed for scissor lifts. It uses sensors to monitor the operator’s position and stops the machine if it detects a potential entrapment – for example, if the operator is pushed against the control panel. Niftylift’s SiOPS® system operates on a similar principle, using pressure-based detection to halt movement when the operator is forced against the controls.
The EQSS and Niftylift SiOPS® systems are designed to act faster than human reflexes, preventing the kind of unintended inputs – such as continued elevation – that can escalate an already dangerous situation. These examples reflect a wider industry shift towards systems that intervene immediately and automatically when something goes wrong.
Common thread
While many of these systems are still evolving, the common thread between all of them is that they move safety from being something operators are reminded to do, to something machines ensure by default, reducing reliance on habit or memory and making unsafe operation less likely by design.
This is the foundation of what we call ‘safety by design’. It’s the idea that, where possible, risk should be engineered out. While we don’t want to eliminate human responsibility, we have to recognise reality. Behavioural change is slow and uneven. It can unravel in a moment of stress or oversight. That’s why safety systems must be designed to protect people when they are at their most fallible.
Paul Rankin: "The industry is increasingly aligned around the idea that safety should not depend on memory, habit or motivation."
Just as importantly, we must accelerate how quickly those systems become standard, because what we lack most at the moment is a sense of urgency. It should not take a decade for proven solutions to become standard. We must shift from long timelines to a two- or three-year adoption window. The pandemic showed us we can move quickly. If we believe that one fatality is one too many – and we should – then slow adoption is itself a safety risk.
In each case we’re talking about addressing unconscious attitudes towards operator safety. In other words, a culture. We need to expedite this change of habit by automating safety practices via intelligently designed features, but we also need to come together as an industry to ensure that such technologies, once tested and ratified, are adopted as swiftly as possible. A high standard of safety should not be something that gives one company a competitive edge over another; it should be the very foundation of our industry, across brands, across customers and across companies.
That means OEMs (original equipment manufacturers), rental companies, regulators and training bodies must come together to define what ‘safe by default’ really means and move quickly to make it the rule, and not the exception.
Already we are seeing this happen. Numerous contractors and clients are now mandating the use of intelligent anchor point systems like Harness ON™, making them a requirement on certain sites or projects. This marks a clear shift in expectations, from relying on voluntary compliance, to making machine-automated safety a baseline condition for work at height.
At the same time, as mentioned above, manufacturers and rental companies are developing their own built-in safety systems, further embedding safe operation into the design of equipment.
Taken together, these developments show an industry increasingly aligned around the idea that safety should not depend on memory, habit or motivation. This is not about removing human responsibility. It’s about meeting human reality with systems that are forgiving when people are fallible. And it’s about using the tools already at our disposal, not waiting until after the next incident to act.
So, let’s get the people who can deliver that in a room – and get it done in two years, not 10.
For more information see: nationwideplatforms.co.uk/en-gb
linkedin.com/company/nationwide-platforms
facebook.com/NationwidePlatforms
T. +44 (0)345 745 0000
Paul Rankin is CEO of Nationwide Platforms
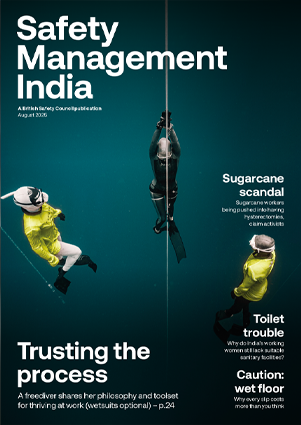
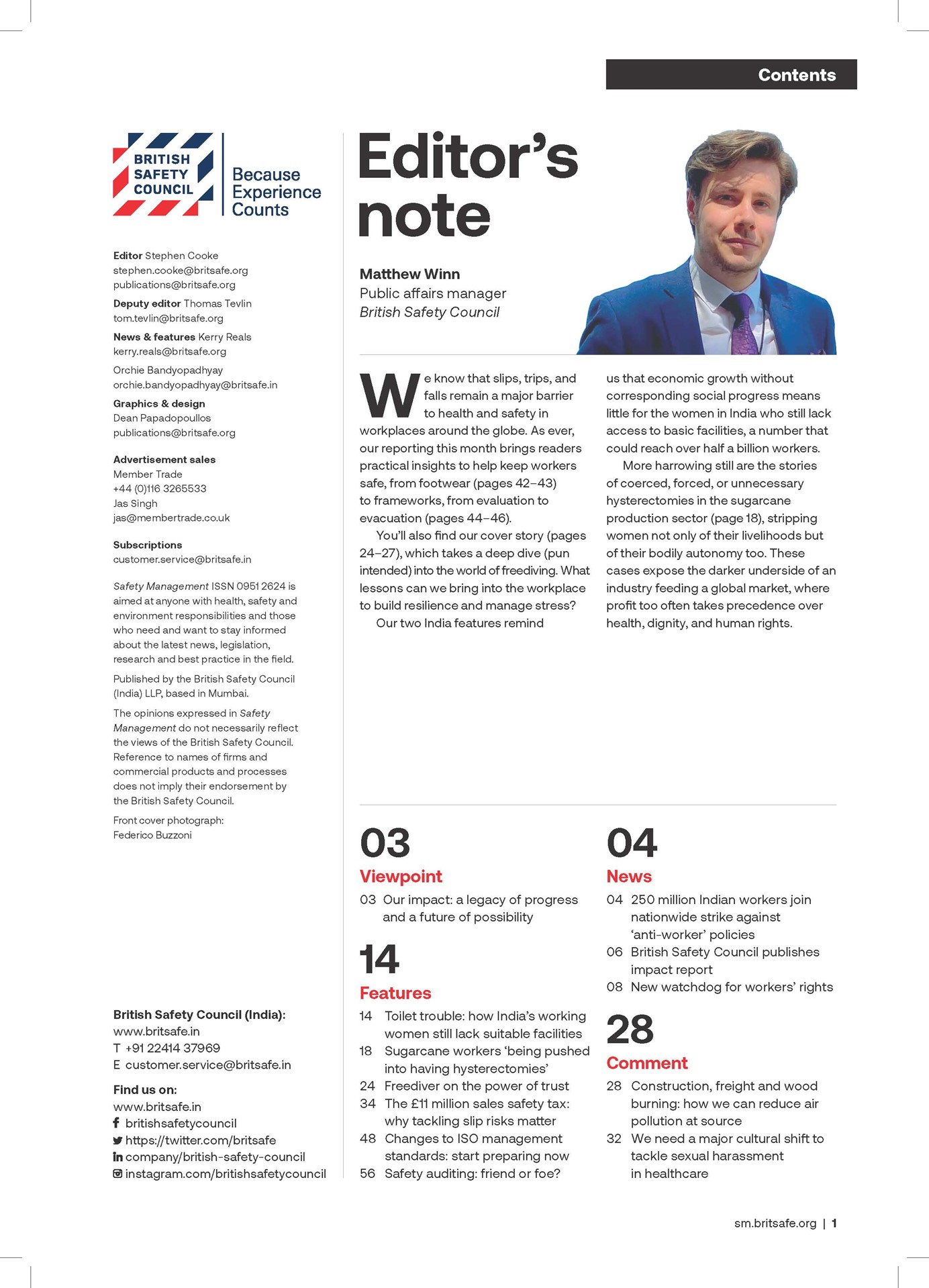
FEATURES
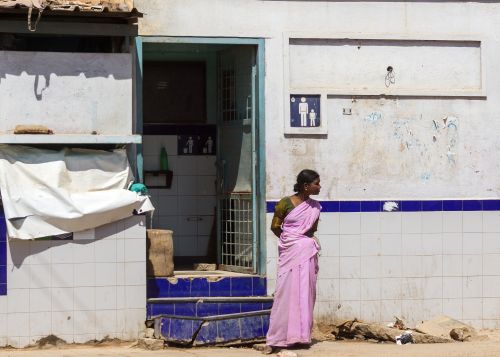
Toilet trouble: how India’s working women still lack suitable facilities
By Orchie Bandyopadhyay on 11 August 2025
Despite government efforts to construct hundreds of millions of toilets across India in recent years, female workers in informal sectors like street vending, construction and agriculture still struggle to find safe and clean sanitary facilities, restricting their earning power and placing their health at risk.
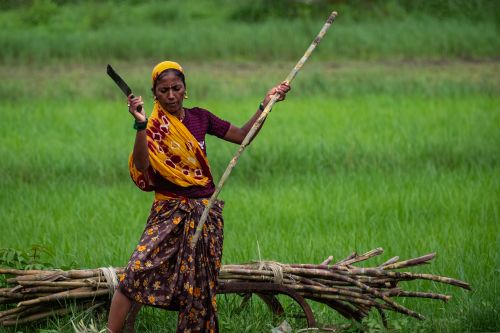
A bitter harvest: female sugarcane workers ‘pushed’ into having hysterectomies
By Orchie Bandyopadhyay on 11 August 2025
The practice of female sugarcane workers in Maharashtra state undergoing unnecessary hysterectomies, in part driven by a financial need to avoid sick days due to menstrual problems and pregnancy, still persists, allege campaigners, despite a state government-commissioned report in 2019 urging greater action to eradicate it.