Health and safety audits provide vital insights into the most effective ways of improving an organisation’s safety performance. However, to get the most from the audit process, it is vital a company is open about its safety performance and systems, and happy to hear ideas for improvement, explains Suresh Tanwar, senior head of audit and consultancy at British Safety Council India LLP.
Features
Safety audits: a powerful tool for keeping everyone safe at work
What does a typical occupational health and safety (OHS) audit for a British Safety Council customer involve?
An OHS audit by the British Safety Council – such as our Five Star Occupational Health and Safety Audit – goes beyond simply asking a company’s safety managers, directors and rank-and-file workers a series of questions about the organisation’s approach to managing OHS risks. It involves actively listening to understand the context behind the responses and asking for – and carefully reviewing – various evidence (such as documentation), to ensure the accuracy of the statements made by the people the auditor has interviewed. Depending on the duration and scope of the audit, the British Safety Council auditor may also offer practical suggestions – such as recommending ways of carrying out specific work tasks in a safer manner.
Also, the process doesn’t end with the audit itself. The British Safety Council provides follow-up consultancy to support organisations to address any areas for improvement highlighted by the audit. These consultancy sessions are not about delivering ready-made solutions to OHS challenges but are instead designed to get the company and its OHS team thinking about the best ways of closing any gaps in their OHS policies, systems and approaches identified during the baseline audit. The approach generally involves the auditor highlighting examples of good OHS practice that the company can learn from and adapt to their own operations.
Every audit begins with an opening meeting and concludes with a closing meeting. At the closing meeting, the auditor presents a summary of the key findings of the audit – highlighting both the strengths of the company’s OHS risk management policies, systems and practices and opportunities for improvement that will further protect workers and others, like members of the public, from OHS risks.
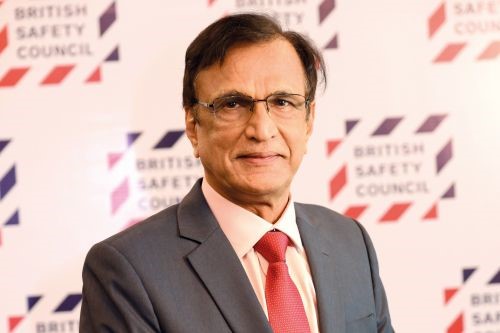
What difficulties does an auditor face when conducting a systematic assessment of a company’s work environment to identify possible hazards and evaluate the effectiveness of the current OHS risk controls?
Any OHS audit, including a British Safety Council audit, is based on a sampling approach, which involves examining a sample of the organisation’s hazards, risks, policies and risk controls. The average duration of an audit is typically four to five days, so it is not possible or viable to inspect every nook and corner of a work site alongside the company’s safety team, directors, departmental managers and staff, or to examine all the OHS processes, policies and systems in exhaustive detail with equal focus. As a result, there’s always a possibility that certain aspects of the company’s operations may not be fully assessed, considered or examined during the audit.
There are also potential challenges for the auditor in relation to the client’s level of transparency and approach to disclosure of information. Some clients may be reluctant to disclose information related to serious injuries, fatalities, near misses and corresponding incident investigation reports. This can create difficulties for the auditor because they may not have the full picture of OHS at a business, which can potentially affect the quality, accuracy and usefulness of both the audit itself and final audit report.
How does British Safety Council’s Five Star Occupational Health and Safety Audit work? What does an organisation receive from the audit, in terms of outputs, recommendations, advice, praise, reassurance, help etc?
The process for a Five Star Occupational Health and Safety Audit begins well before the actual delivery of the audit. The auditor firstly establishes contact with the client to explain the audit process and to share a detailed schedule outlining the elements of the company’s OHS system that will be reviewed and on what dates and timescales.
The audit officially begins with an opening meeting, during which the scope of the audit is shared with the client team. This session also provides an opportunity for the client to present their health and safety journey, including key initiatives and milestones towards OHS excellence.
The core of the audit involves three key activities including: (i) documentation review; (ii) site walk-throughs, during which the auditor interacts with people like the safety manager, supervisors and employees and asks relevant questions; and (iii) discussions with senior leadership, particularly the director or senior manager in overall control of the site, to understand the company’s strategic direction on OHS and the extent and effectiveness of leadership commitment to excellent health and safety performance.
The audit concludes with a closing meeting.
Following the audit, the auditor has up to 10 days to complete the audit report. The draft report is then submitted to the British Safety Council’s Audit and Consultancy team (headed by myself) for quality assurance (QA), to ensure its technical accuracy and consistency. Following the QA process, the report is passed to the British Safety Council’s Operations team for final formatting and is then shared with the client.
The entire reporting process is completed within 28 days from the final day of the audit.
This is how the complete cycle of the Five Star Occupational Health and Safety Audit takes place.
In India, most companies opt for a pre-audit, also known as a Gap Assessment, before undergoing the more comprehensive Five Star OHS Audit. Both types of audits follow the same British Safety Council specification, and the specifications are valid for a year, as they are regularly updated to reflect ongoing international best practice developments in OHS management, and any relevant changes to Indian OHS legislation.
However, a Gap Assessment and a Five Star OHS Audit have different purposes and different outputs. A pre-audit (Gap Assessment) is designed to highlight any areas that require improvement before undergoing the more detailed Five Star OHS Audit. A Gap Assessment is generally a desktop exercise (i.e. an examination of paperwork, records etc., rather than formal on-site interviews with key individuals). It uses a RAG (Red–Amber–Green) rating system to assess the company’s OHS systems and performance and includes recommendations for improvement, where necessary.
On the other hand, the Five Star Audit is a much more detailed and comprehensive examination of the company’s OHS system (including on-site visits and interviews), and provides detailed recommendations and scores for 50 OHS elements under four separate sections. Each section is given a score, and there is also an overall score and rating for the company, based on the overall results of the audit across the four sections. A score of 92 per cent or above qualifies for a Five Star rating.
Both reports begin with an Executive Summary, which highlights examples of good and best practices and high-level areas for improvement.
What role does technology play in modern OHS audits in India? Are there any innovative tools or methods British Safety Council uses?
At British Safety Council, we upgrade our Five Star OHS Audit specification annually to ensure it remains current, relevant and aligned with the latest Indian and international industry trends, best practice and legislation. The auditor uses a specially designed audit tool to ensure they are assessing all the appropriate areas and aspects of the OHS system and a specially designed report template has been developed to ensure consistency in the quality, type and format of information, ratings and feedback provided to the client.
During the audit, some companies showcase how they have deployed technological interventions and innovations to improve OHS. For example, at one facility management site, the company eliminated the need for personnel to manually clean the building’s external glass façade using automation, employing specialist cleaning equipment and robotic systems.
Do cultural factors, such as attitudes towards OHS among company management and employees, impact the effectiveness of the OHS audits you undertake for British Safety Council clients?
Yes, cultural factors can definitely have an impact on the effectiveness of the audit.
Sometimes, there are restrictions on the company sharing OHS data with the auditor, and the auditee team may need to seek permission from senior management before providing certain information. Also, documentation is not always organised systematically, which can lead to delays as the site’s safety team and others search for the required documents in response to auditor queries. This can have a negative impact on the audit schedule, shortening the time available to examine other aspects of OHS.
In your opinion, to what extent are companies across India complying with Indian OHS legislation, such as the Factories Act 1948? Where businesses are failing to comply with the law, and failing to properly manage OHS risks, what are the key reasons for this?
Clearly, responsible employers do not wilfully set out to avoid complying with the Factories Act and other central government-enacted laws and state-level rules around OHS. However, the fact remains that a significant number of Indian companies are failing to fully comply with both the spirit and full requirements of OSH legislation. One reason for non-compliance is poor awareness and understanding of the requirements of the law, as some employers struggle to comprehend the specific clauses and requirements of specific OHS legislation.
To ensure full compliance with OHS legislation, British Safety Council recommends companies carry out a full assessment of the applicable OSH laws and provide (or arrange) training so relevant members of staff with management responsibilities understand how to ensure compliance ‘on the ground’.
If a business is struggling with this process, due to – for example – a lack of knowledge and competence around OHS legislation and best practice, they can engage help from external consultants.
Which industries do you most frequently audit, and which ones pose the greatest OHS risks?
British Safety Council has carried out OHS audits in almost all Indian industries, excluding the mining sector. Arguably, among the sectors we have audited, the steel manufacturing industry presents the greatest OHS risks due to the hazardous nature of the work processes and the challenging working environment. Another industry that poses a significant risk is construction, in part because of the dynamic nature of construction sites, with the type of hazards and the extent of the risks changing on a daily or even hourly basis.
How effective is the management of OSH risks in the factories of automotive supply chain companies and automobile manufacturers? Does the automotive manufacturing industry need to improve its OHS systems and performance, and if so, how?
Automobile manufacturing operations generally fall into the bracket of low to medium risk, although there is the possibility of serious consequences should a fire break out in an automotive paint shop. Automotive paint spraying operations also pose significant risks to workers’ health, such as inhalation of harmful substances leading to conditions like asthma, due to potential exposure to chemicals and isocyanates found in some paints.
In factories where vehicle parts are manufactured for supply to larger automobile manufacturing companies, there has been a history of serious injuries and fatalities. There are a variety of reasons for this, including inadequate provision of financial and staffing resources for OHS by the company management, resulting in a lack of competent safety staff with the knowledge and time to ensure the safety of production line workers.
Another cause is risk-taking behaviour by employees, often due to a lack of suitable safety training.
Are there any particular OHS issues or challenges that are unique to India due to its socio-economic conditions or work culture?
India does have some unique OHS challenges arising from its socio-economic conditions and prevailing work culture.
For example, many companies rely heavily on contract workers, many of whom have limited formal education and have received little safety training. The low level of risk perception among contract workers often results in them unknowingly putting themselves and others in harm’s way.
Also, in a significant number of companies, there is a high turnover of workers, which makes it difficult to ensure workers receive the appropriate training. Managers often find themselves having to provide training for new starters on a monthly, or even weekly, basis and it can be very difficult to find the time and resources for this.
There can also be problems with workers taking short cuts with safety and disregarding safety instructions and rules, despite being given training on how to follow the rules.
In addition, societal hierarchies can sometimes have a negative influence at work, creating obstacles to improving safety performance and cultivating a strong safety culture.
For instance, in some workplaces, employees are not empowered or encouraged to speak up about safety problems or stop work if they are faced with unsafe conditions, even when there is a clear risk of serious injury.
However, it is vital that employers create an open culture where staff are encouraged to report safety problems and stop work immediately if there is an OHS risk, without fear of sanctions such as disciplinary action or loss of employment. When workers feel safe to voice concerns without fear of retribution, the level of trust and transparency across the business increases and paves the way for improving the company’s safety culture. This is the essence of psychological safety, where workers believe that they are able to speak up with ideas, questions, concerns and mistakes, and won’t suffer negative social or professional consequences as a result.
Maharashtra’s Industry, Energy, Labour and Mining Department recently amended the law to require factories in Maharashtra state carrying out certain hazardous processes (or handling and creating certain hazardous, explosive, inflammable or toxic substances), which employ 50 or more workers to undergo a formal OSH audit by a certified independent professional or an institution recognised by the state government. Previously, the threshold for an audit was factories with 250 employees. Do you believe this change was necessary and should have been implemented sooner? Do you think this change will improve OHS in Maharashtra’s factories? Do you think this move should be adopted by all States and Union Territories?
In my view, the deciding factor for most appropriate frequency and scale of OHS audits – whether they be voluntary audits arranged by a company or requirements set out in legislation – is the level of risk posed by the industry’s activities or the activities at a specific workplace.
In general, I would argue that in high-risk sectors – such as mining, construction and steel manufacturing – OHS audits are not just advisable, they are essential. These sectors also typically employ large workforces, often well above thresholds like 50 or 250 employees. In all cases, decisions about the need for an OHS audit should be based on the level of risk posed by the work or the workplace.
A safety audit is a very powerful and proactive tool for identifying both areas of strength and areas requiring improvement within a company’s safety system. To be effective, audits must be conducted by competent and experienced auditors. The audit findings and recommendations provide a very useful roadmap for duty holders (i.e. the employer) to address gaps in their OHS systems and to ensure they sustain their high performance in areas where they have been found to excel. The entire audit process and report helps to ensure continuous improvement in OHS and ongoing, sustained high levels of safety performance.
How do OHS standards in India compare with global OHS standards? Are there any gaps or areas where improvements are required?
In terms of recognised best practice in OHS management, at international level, OHS standards are very stringent and agile, and are continuously being improved and refined in line with what is considered to be the most effective ways of managing risks. Therefore, businesses wishing to achieve the highest standards of OHS are always looking to recognised global best practice approaches to OHS, and comparing their current systems and updating them where necessary.
In fact, throughout my career in OHS across various organisations, I have observed that multinational companies are considerably more advanced, both in terms of their understanding and achievement of high safety standards and their compliance with laws and adoption of internationally-recognised best practices.
For instance, Lockout-Tagout (LOTO), a critical procedure that ensures machinery and energy sources are properly shut off and cannot be restarted unexpectedly during maintenance or repair work, was routinely implemented in a multinational company
I worked for as early as the late 1980s. In contrast, even by 2005, many Indian manufacturing sites had yet to adopt LOTO practices with the same rigour, primarily due to limited duty holder awareness of its value and how to adopt it, and a lack of emphasis on its importance across Indian industry.
Similarly, in the management of fire risks at work, global organisations tend to achieve much higher standards compared with many Indian companies. So, this again highlights a gap in safety practices between a significant number of Indian companies and leading multinationals, who are often leaders in fire risk management at work.
In your opinion, how effective is the current OHS legislation in India in protecting workers? Are there any areas that need reform?
The Directorate of Industrial Safety and Health (DISH), formerly known as the Factories Inspectorate, has sufficient legal powers to ensure the protection of workers. If a company is found violating safety laws, they can be subject to fines and penalties.
In the past, these fines and penalties may have been considered nominal, but they have become considerably more substantial in recent years.
DISH enforces compliance with OHS laws proactively through regular inspections. There are also special provisions in the Factories Act requiring duty holders to take extra steps to ensure workers’ OHS when the work involves hazardous processes and dangerous operations. A failure to comply with these more stringent requirements can also result in more stringent penalties.
If there is a safety incident and a worker is injured, the Workmen’s Compensation Act comes into effect. This places a duty on employers to cover the cost of compensation to workers suffering certain injuries in certain industrial incidents. Historically, the levels of compensation awarded under this Act were quite low, but they have increased quite substantially in recent years. In turn, this has placed greater pressure on employers to avoid compensation payouts by taking more effective measures to prevent accidents at work.
What should be the top priority for businesses in India when it comes to improving OHS?
Companies need to understand that OHS is not a hindrance or a burden; it is an investment that will help a business succeed.
For instance, keeping workers safe enables employers to retain skilled and loyal employees, who can contribute to the ongoing success of the business. In addition, preventing accidents avoids the need for management time to investigate and correct safety problems; and means the company avoids financial penalties in the form of fines and compensation payouts to injured workers.
Good safety performance also means the company avoids the negative publicity associated with accidents, injuries and fatalities, which can result in loss of business from customers and supply chain partners, who do not want to be associated with a business with a poor safety record.
However, for a company to excel at OHS management, health and safety must be seamlessly integrated into all aspects of business planning and decision-making.
This shift in mindset must begin at the top. When senior leaders champion safety, set the tone and allocate sufficient financial and staffing resources to OHS, the attitude cascades down through the organisation, and everyone at all levels comes to understand the importance of implementing, adopting and following effective OHS policies and systems.
Ultimately, the goal for any business is zero incidents. Every initiative and programme should be designed with the core objective that no individual is injured or made ill while performing their work.
If duty holders address all three ‘Ps’ appropriately – People, Process and Plant – they will succeed in improving their organisation’s OHS performance.
What inspired you to become an OHS auditor, and how did you begin your career in this field?
I began my working life an engineer specialising in general maintenance and general engineering projects.
During the 1990s, while working at the Mumbai site of American multinational Johnson & Johnson, OHS management began to become a prominent aspect of my role. The management of OHS risks very quickly turned into a passion, so I approached the vice president of operations and expressed my desire to move into the OHS department. A few days later, he told me that I would be taking over the safety role at the Mumbai site with immediate effect.
After taking on the post, I immediately realised that the company had adopted – and expected – the highest standards of safety, driven by its US roots. For example, Johnson & Johnson had implemented – and demanded – the highest possible fire safety protocols across all sites globally, including my site in Mumbai.
Also, the company had developed and implemented a ‘zero access’ machine guarding system (they subsequently trademarked this approach), which ensured that no one entered a machine enclosure unless the machine was fully isolated to prevent the system being restarted or re-energised and putting them at risk of serious injury. Both of these approaches were far ahead of their time.
From that point onward, my career evolved steadily. I progressed from a site-based safety role to leading corporate safety and health, safety and environment functions, eventually becoming group head of health and safety for Tata Group, before retiring from this post in 2018. I then joined British Safety Council as an OHS auditor and consultant and, within a year, was offered the permanent role of head of audit and consultancy.
It’s been an incredibly eventful, fulfilling and enriching journey, spanning over 25 years.
What has been your most rewarding experience as an OHS auditor?
It is very rewarding when the auditee learns from the interaction they have with myself (and between myself and others I speak to at the company), during the audit process and gets real benefits from the detailed report we produce following the audit. I get immense satisfaction when the audited company can further improve their OHS systems and performance thanks to my advice.
If you had to give an employer a single bit of advice on how to improve OHS, what would it be?
I would recommend that duty holders carefully consider any recommendations that emerge from an OHS audit, and remain open minded to any suggestions for improvement, and criticisms.
The key to a business getting the maximum value from an OHS audit (and therefore getting advice that will help them improve their OHS performance), is to be transparent and let the auditor have genuine visibility and insight into all relevant aspects of OHS at the site.
The company being audited should remember that the auditor deploys all their qualifications, experience and knowledge of good and bad practices from a variety of industries when conducing an audit, and ultimately is there to help the company improve and excel at OHS management.
So, the people who provide information to and interact with the auditor should remember never to try to stage-manage the interactions, or become defensive if any criticisms or errors are highlighted, as the auditor’s only aim is helping the company to become even better at keeping workers safe and healthy at all times.
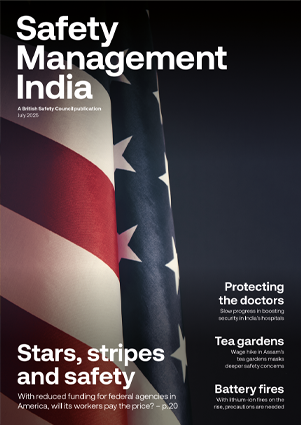
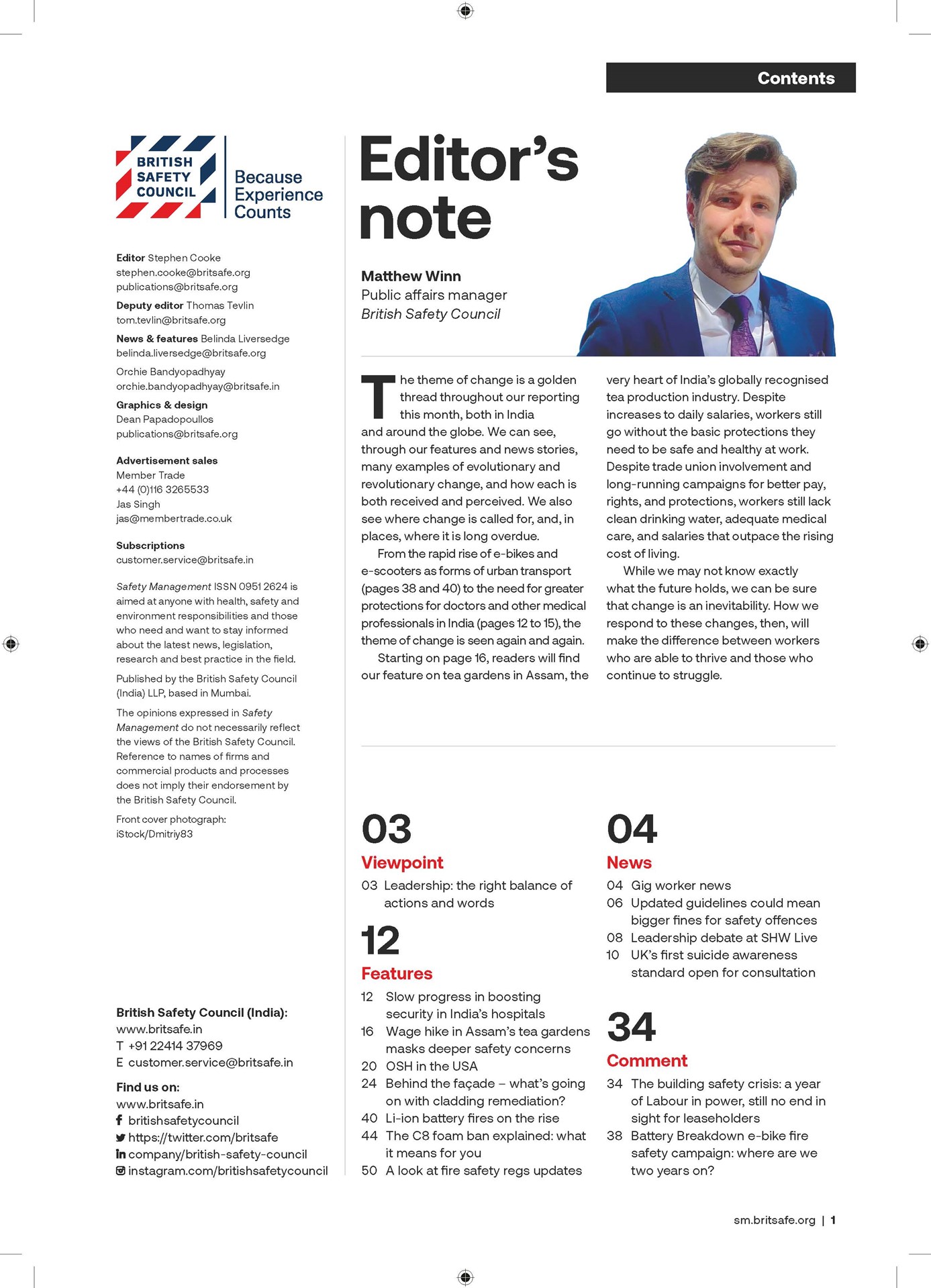
FEATURES
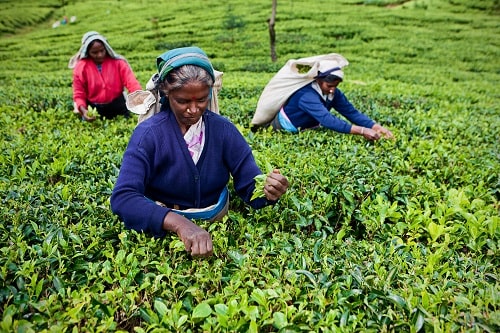
Assam’s tea gardens: the battle for decent working conditions continues
By Orchie Bandyopadhyay on 14 July 2025
Although Assam’s state government recently announced a pay rise for workers in state-run tea plantations, trade unions say the industry’s workforce still faces poor working and living conditions, despite years of protests and demands for improvements.
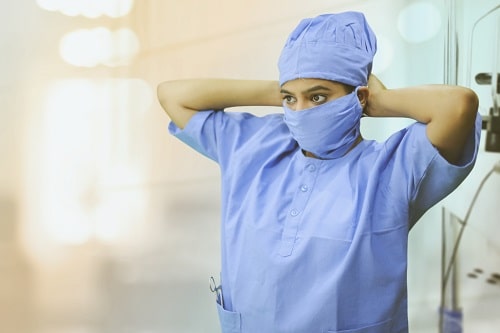
India’s medical sector – ‘doctors still at risk of violence’
By Orchie Bandyopadhyay on 14 July 2025
Almost a year after the rape and murder of a young female doctor at a Kolkata hospital horrified the nation, commentators say progress has been painfully slow in improving the safety and security of many hospitals and doctors’ living accommodation.
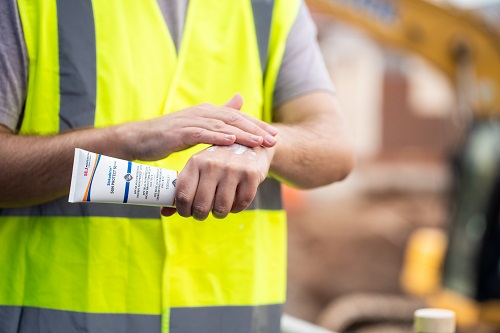
Facing the facts: protecting your outdoor workforce from UV exposure and skin cancer
By SC Johnson Professional on 11 July 2025
With outdoor workers at significant risk of skin damage, ageing and cancer due to exposure to the sun’s UV rays, it’s essential that employers in sectors like construction and agriculture create a working environment where sun safety precautions become the norm, rather than the exception.